Asphalt is the pavement of choice for highways, roads and parking lots around the world. It’s an ecofriendly material that can be recycled and has a long lifespan which reduces resource consumption and waste.
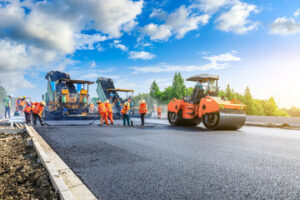
It’s made from a combination of aggregate materials like crushed stone, gravel and sand and a substance called bitumen that holds it all together. Different types of asphalt are created for different climates and road conditions. Contact Asphalt Paving Charleston SC for professional help.
Asphalt paving is a versatile and popular choice for building roads, parking lots, train tracks, airport runways, bike lanes, sidewalks, and play and sports areas. The material is a mixture of aggregates, binders, and fillers that are used to create a strong and durable surface. It is also more environmentally friendly than concrete paving because the materials can be recycled and reused.
Choosing the right asphalt mix for your project depends on its purpose and expected traffic volume. High-traffic areas require pavement that can withstand the load of heavy vehicles over a long period of time. This requires an asphalt mix with a higher density and stronger binder content than low-traffic areas.
Aggregates are crushed stone, sand, gravel, or slags that provide structural support for the asphalt mix. They can be natural, such as crushed granite or sandstone, or made from recycled materials like rubber tires, steel and iron manufacturing byproducts, and construction and demolition debris. Asphalt binder is a sticky substance that binds the aggregates together and helps form a solid pavement. The most common binder is bitumen, but there are several newer options, including recycled asphalt, stone matrix asphalt (SMA), and bio-based binder.
A flexible asphalt mix adapts to local climate conditions, including extreme temperature variations. The material’s flexibility helps it resist rutting in the summer and freezing thawing cycles in the winter.
The elasticity of asphalt pavements can also reduce the amount of energy used to maintain them, making it more environmentally friendly than other paving materials. It also reduces greenhouse gas emissions, such as carbon dioxide (CO2) and nitrous oxide (NO2). Unlike other paving materials, asphalt also allows for faster and easier repairs.
Preparing the Area
Unlike concrete, which can be poured directly onto your existing driveway or parking lot, asphalt must be prepared first. This involves removing all vegetation and old pavement, and it also includes grading the site. This is crucial for getting the right drainage and preventing future problems like water potholes, heaving, and cracking. Our team uses technology like automatic motor graders and laser-guided transits to make sure that the base of your new asphalt is as smooth as possible.
This is important because the sub-base layer provides a foundation for the entire pavement, and it needs to be strong and stable. Without a proper sub-base, your asphalt won’t be able to stand up to the heavy loads it will need to support. In addition, the sub-base helps prevent water damage from thawing and freezing during winter.
Once the sub-base layer is laid, it’s time to put down a “proof roll” – this will ensure that the underlying surface is strong enough to support the asphalt that’s to come. If the proof roll reveals any soft areas, workers will dig down and replace them with more durable aggregates.
The next step is to lay down a binder layer – this is made of aggregate materials mixed with oil. The mix is then rolled and compacted. Typically, new asphalt is installed over old concrete or asphalt surfaces, so butt joints are installed to ensure a seamless transition.
Then it’s time to install the asphalt itself. This is done by using a paver that spreads the material over the surface and then pressing it down with rollers to compact it. Once it’s rolled, the asphalt must sit for 24 hours to cool and harden. This will prevent cars from driving on the asphalt too soon, which can cause premature damage.
Installation
Asphalt is a durable and versatile material that can be used for roads, driveways, parking lots and more. It has many advantages over concrete, including less weight, lower installation costs and better traction for vehicles. It also requires less maintenance than other types of paving materials and is easy to repair when needed. Asphalt can be used in both new construction projects and as a replacement for existing pavement.
Asphalt paving is environmentally friendly, as it uses recycled materials and reduces the need for new asphalt production. It also uses energy-efficient technologies that optimize production processes and minimize waste. Additionally, asphalt pavements can be recycled after use to extend their lifespan and save money on future paving costs.
The asphalt paving process begins with draining and removing any existing pavement, if necessary. Then, the base is built and compacted to ensure a solid foundation for your surface. Once the base is ready, the paving material is placed. Asphalt is typically made up of two ingredients – bitumen and aggregates, such as gravel or sand. The mixture is heated to over 300°F, allowing it to be easily spread and laid on top of the base.
Another benefit of asphalt is that it can be easily marked with lines and other markings, making it easier for drivers to navigate a road or parking lot. These markings stand out against the black color of asphalt, which helps keep them visible even in low-light conditions. This helps increase safety and decreases the risk of accidents.
Compaction
The primary goal of compaction is to densely pack the asphalt material, reducing air voids and creating a durable surface that will withstand traffic and the elements. Achieving proper compaction requires a combination of specialized equipment and skills.
The asphalt mixture needs to be at the ideal temperature to compact properly. As it leaves the paver screed, it is usually around 300 degrees Fahrenheit, but once it reaches the ground it will quickly cool down to a temperature that makes it stiff and difficult to compact. The ambient temperature and wind speed also affect the rate of cooling, as does the thickness of the layer being paved.
Once the layer of asphalt has reached its target temperature, the paving team can begin to compact it using a variety of machinery. Static steel-wheeled rollers, vibratory rollers, and pneumatic tire rollers all play a role in achieving optimum density. Each machine has its own unique strengths and weaknesses, so selecting the right one for the job is crucial. A reputable asphalt contractor will have the expertise to choose the best machines and understand how to operate them for optimum results.
In addition to adjusting machine settings, paving contractors need to carefully monitor the process and adjust for environmental factors. A failure to do so could lead to raveling, a deterioration that causes the loose surface to separate from the underlying material and create an unattractive, rough road. By paying close attention to the details, a quality asphalt contractor can achieve a high level of compaction that will stand up to traffic for decades. This helps the paving company fulfill its fiscal responsibility and keeps motorists safe and happy on the roads.
Curing
Asphalt is a durable material that requires proper curing to transform from soft asphalt into a hard, stable surface. The curing process depends on several factors, including weather, temperature, and the type of asphalt. Understanding these factors can help contractors and property owners ensure that the asphalt is properly cured and ready to use.
When it comes to making asphalt, there are two main ingredients: aggregates (like rocks, gravel, and sand) and bitumen. The aggregates make up about 95% of the material, while bitumen is a dark, sticky, petroleum-based substance that holds everything together. Before the paving process begins, all of these materials are weighed using a belt weighing instrument to get an accurate measurement of their weight. Then, the components are dried to remove any moisture that could affect the final product. The aggregates are then sifted and stored in silos, while the bitumen is kept in heated tanks until it is needed.
Once the asphalt is mixed, the bitumen is added to the aggregates and incorporated into the pavement. It is very important that the bitumen is of a high quality to ensure that it will set up well and last long. One way to test the quality of an asphalt bitumen is to analyze its residual oil content, or REOB. REOB can be measured by a simple laboratory analysis, although the composition of REOB can vary widely between different producers and even within the same producer on the same day.
It is also important to note that the paving should be sealed immediately after it has been cured. This will protect the pavement from damage and prevent any cracking in the future. Cracks can often begin at the edges of an asphalt surface, especially on rural roads or driveways, and if not addressed early on can lead to significant issues down the road.